Optimierung und Produktion eines Boot Impeller für Jet Drive
Hightech für maximale Effizienz in der Marine-Antriebstechnik.
Anforderungen an die Marine-Antriebstechnik
Bei Diry Industries sind wir darauf spezialisiert, Bauteile nicht nur präzise zu reproduzieren, sondern durch den Einsatz modernster Technologien und Materialien zu optimieren. In diesem Beitrag zeigen wir, wie ein optimierter Impeller die Leistung eines Jet-Antriebssystems nachhaltig steigern kann und welche Schritte dafür erforderlich sind.
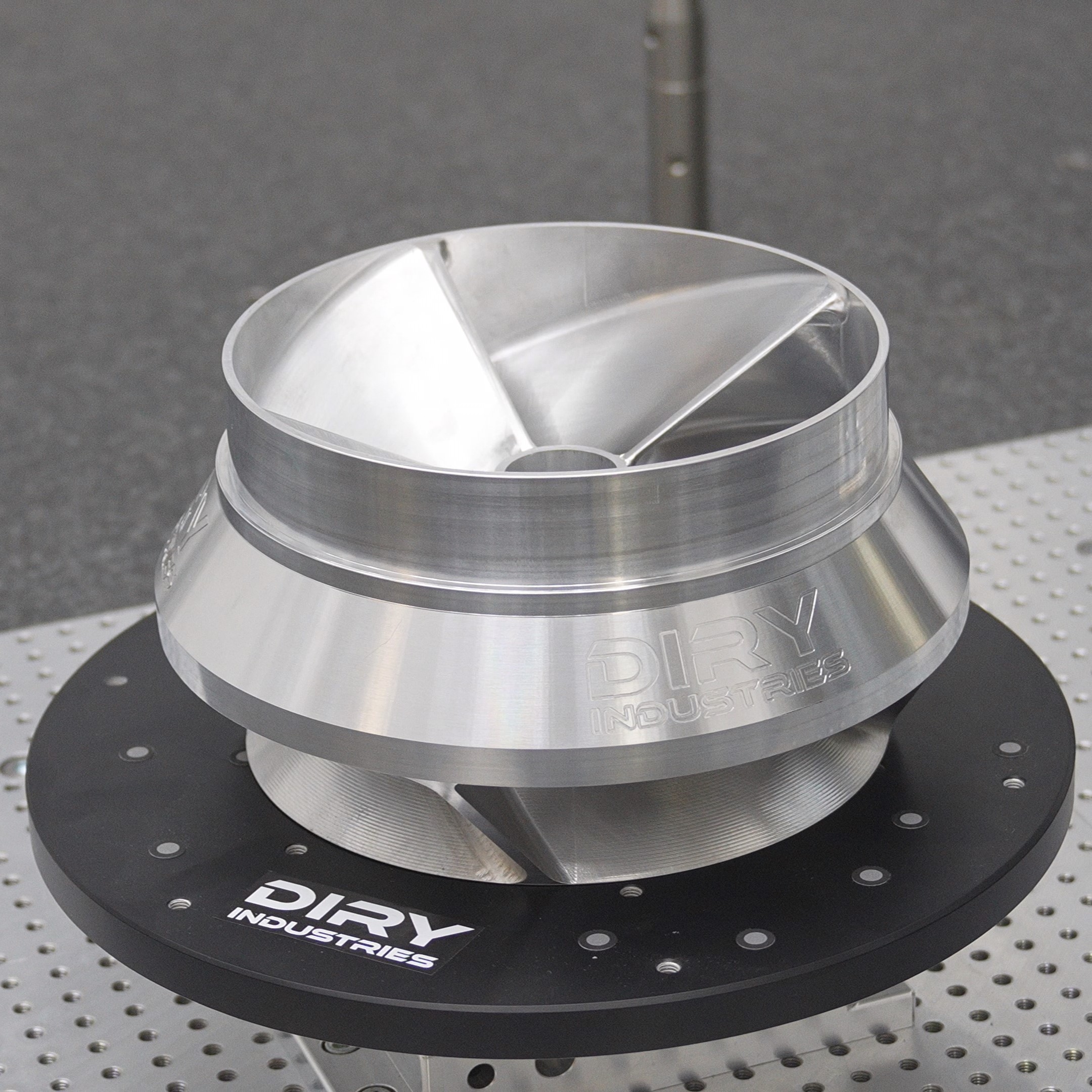
Grundlagen: Warum der Impeller so wichtig ist – Die Funktion des Impellers im Jet Drive
Die Funktion des Impellers im Jet Drive
Ein Jet Drive arbeitet nach einem einfachen Prinzip: Wasser wird durch eine Ansaugöffnung aufgenommen, über den Impeller beschleunigt und durch eine Düse ausgestoßen. Dies erzeugt den notwendigen Schub, um das Boot vorwärts zu bewegen.
Der Impeller selbst ist so konstruiert, dass er sowohl den maximalen Durchfluss als auch eine effiziente Beschleunigung des Wassers ermöglicht. Dabei muss er extremen Belastungen standhalten.
Herausforderungen durch Verschleiß und Leistungssteigerung
Im Laufe der Zeit wird der Impeller durch Riefen, Steinschläge und Materialabtrag geschädigt. Zusätzlich stellen modifizierte Motoren – wie in unserem Fall ein 8,6-Liter-V8 mit gesteigerter Leistung – höhere Anforderungen an die Geometrie und das Material des Impellers. Diese Herausforderungen machen eine präzise Anpassung und Fertigung unerlässlich.
Digitalisierung des Impellers: Präzision im ersten Schritt
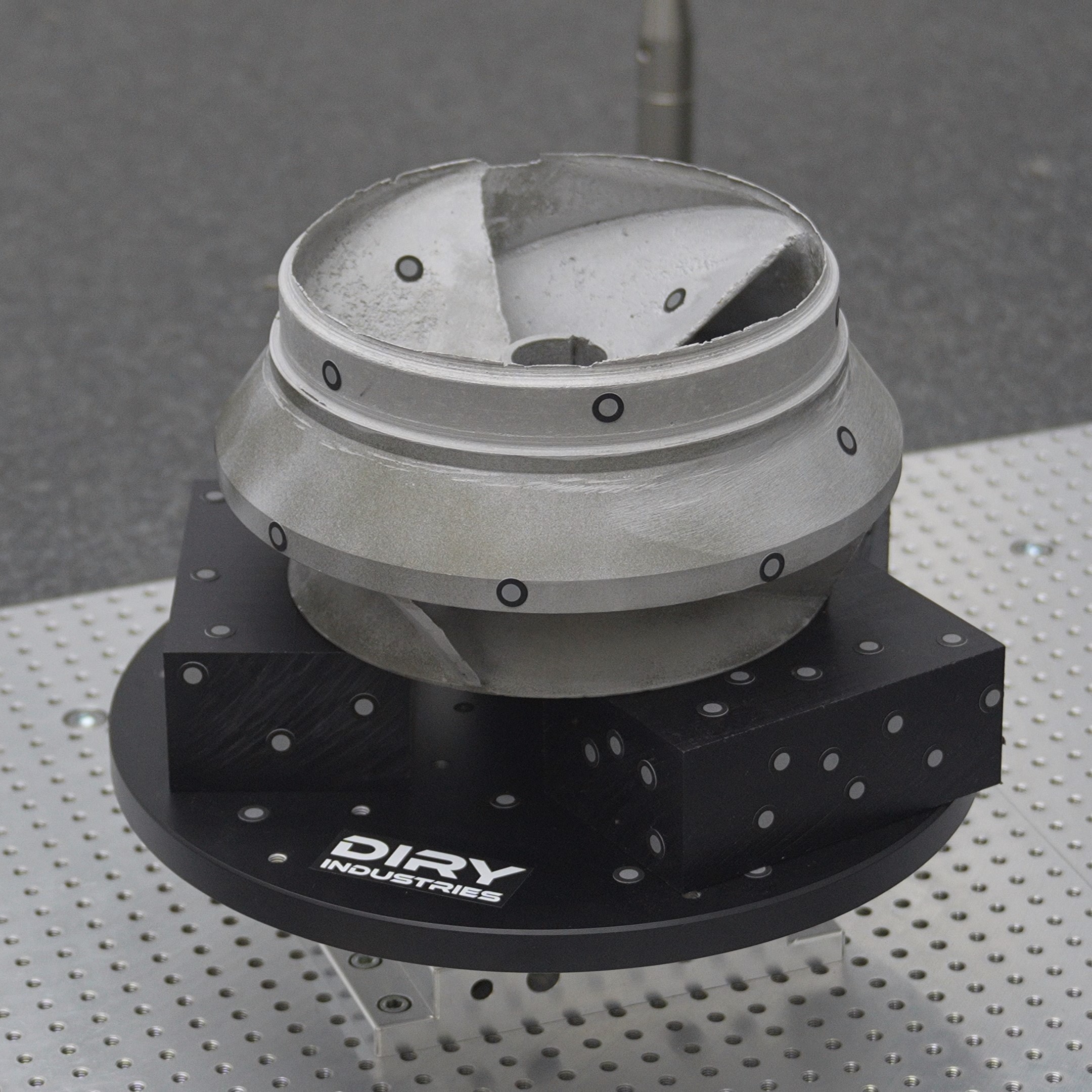
Reinigung des Impellers
Bevor der Impeller digitalisiert werden kann, wird er gründlich durch Glasperlenstrahlen gereinigt. Dieser Prozess entfernt Ablagerungen und Verkrustungen, sodass die Originalgeometrie klar erkennbar ist.
3D-Scanning mit höchster Genauigkeit
Für die Digitalisierung nutzen wir einen hochpräzisen Laserscanner, der mit einer maximalen Abweichung von 20µm arbeitet und bis zu 3 Millionen Messpunkte pro Sekunde erfassen kann. Dieses Verfahren ermöglicht eine exakte Abbildung des Bauteils, einschließlich aller Schäden wie Riefen, Steinschläge und des Materialabtrags durch Kavitation.
Die Punktewolke, die durch den Scan entsteht, bildet die Grundlage für alle weiteren Optimierungs- und Fertigungsschritte.
Reverse Engineering und Geometrie-Optimierung
Auf Basis der Punktewolke wird nun ein parametrisches 3D-Modell erstellt, das Ziel der Rekonstruktion ist es den alten Impeller ohne die Verschleißerscheinungen für die weitere Untersuchung abzubilden.
Analyse der Schwachstellen
Der aufbereitete 3D-Datensatz wird in einer spezialisierten Software für numerische Strömungsmechanik untersucht. Diese Analyse zeigt, wo sich Schwachstellen in der ursprünglichen Geometrie befinden.
Nach jeder Anpassung des 3D-Modells muss dieser Schritt wiederholt werden, um sicherzustellen, dass die gewünschten Verbesserungen erreicht wurden.
In unserem Fall wurden Optimierungspotenziale in zwei Bereichen identifiziert
Ansauggeometrie – Verbesserungen in diesem Bereich reduzieren Strömungsverluste und erhöhen die Effizienz.
Schaufelwinkel – Anpassungen des Schaufelwinkels verbesserten die Förderleistung, insbesondere bei höheren Drehzahlen. Diese Anpassung ermöglicht es, die gesteigerte Motorleistung besser zu nutzen. Für den neuen Impeller entschieden wir uns für eine hochfeste Aluminiumlegierung. Diese bietet im Vergleich zur ursprünglichen Gusslegierung deutlich höhere Festigkeitswerte, hieraus resultiert eine höhere Gestaltungsfreiheit und die Möglichkeit geringerer Wandstärken.
Numerische Validierung des Designs
Das optimierte 3D-Modell wurde erneut durch numerische Strömungsmechanik getestet. Diese Validierung stellte sicher, dass die neue Geometrie den gewünschten Leistungsanforderungen entsprechen.
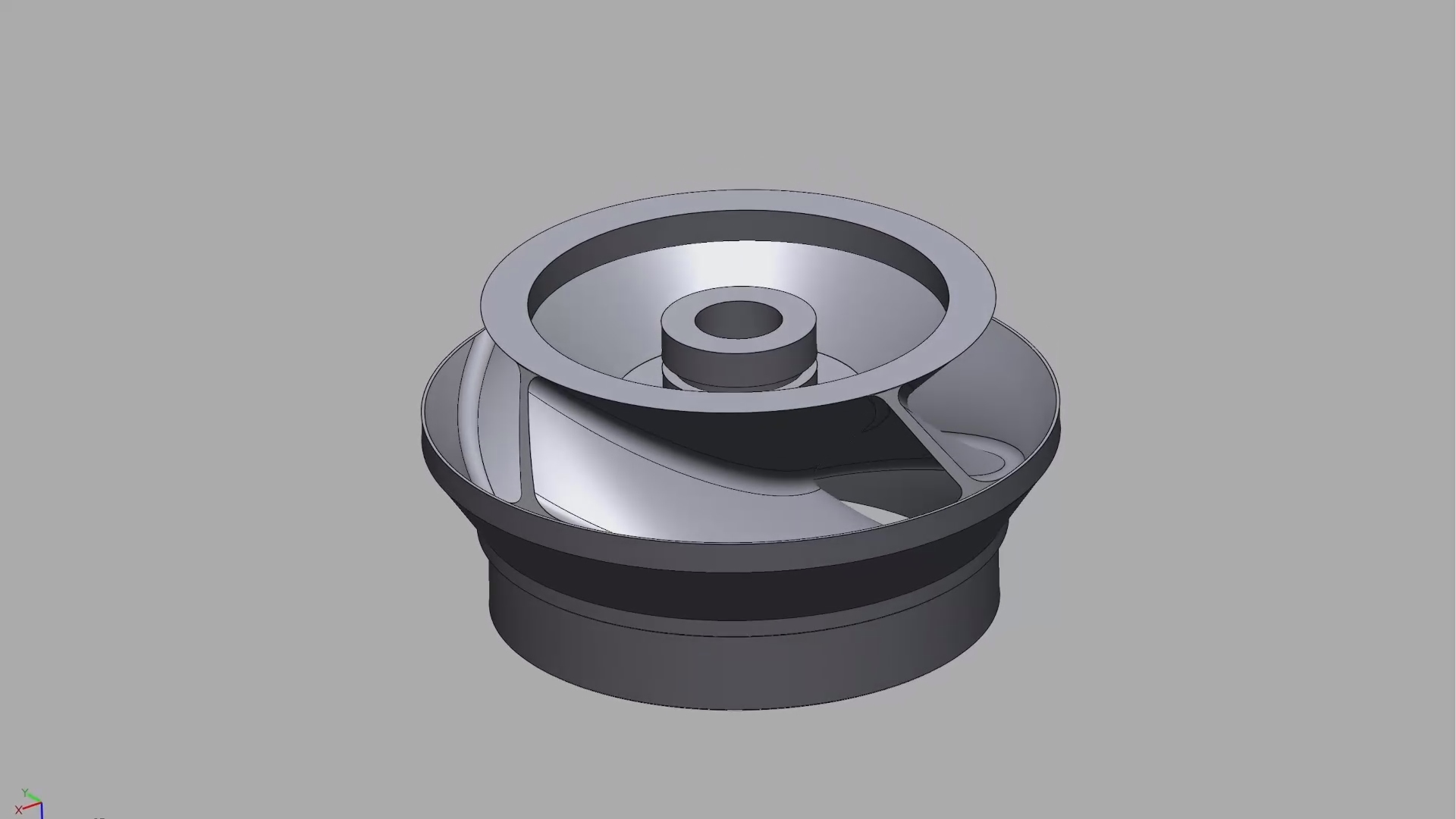
Fertigung des optimierten Impellers
Bei der Fertigung des Impellers setzen wir auf modernste CNC-Maschinen, hier entsteht das Werkstück durch das Bearbeiten eines Aluminium Vollmaterial Blocks.
Im Vergleich zu Guss-Herstellungs Verfahren bietet die CNC-Fertigung klare Vorteile:
Maßhaltigkeit – Abweichungen bleiben innerhalb engster Toleranzen.
Materialfehler – Keine Guss- und Gefüge-Fehler welche negativen Einfluss auf die Wuchtgüte und die Materialeigenschaften haben.
Oberflächenqualität – Glattere Oberflächen führen zu einem geringeren Schubspannungswiderstand.
Unsere modernen CNC-Maschinen sind mit Funktionen ausgestattet, die speziell für die Bearbeitung komplexer Geometrien entwickelt wurden:
Direkte Wegmesssysteme – Diese Systeme garantieren, dass die Bearbeitung innerhalb engster Toleranzen erfolgt.
Hohe Steifigkeit – Dies minimiert Vibrationen und sorgt für eine gleichmäßig hochwertige Oberflächenqualität.
Temperaturkompensation – Schwankungen durch Wärmeentwicklung werden automatisch ausgeglichen.
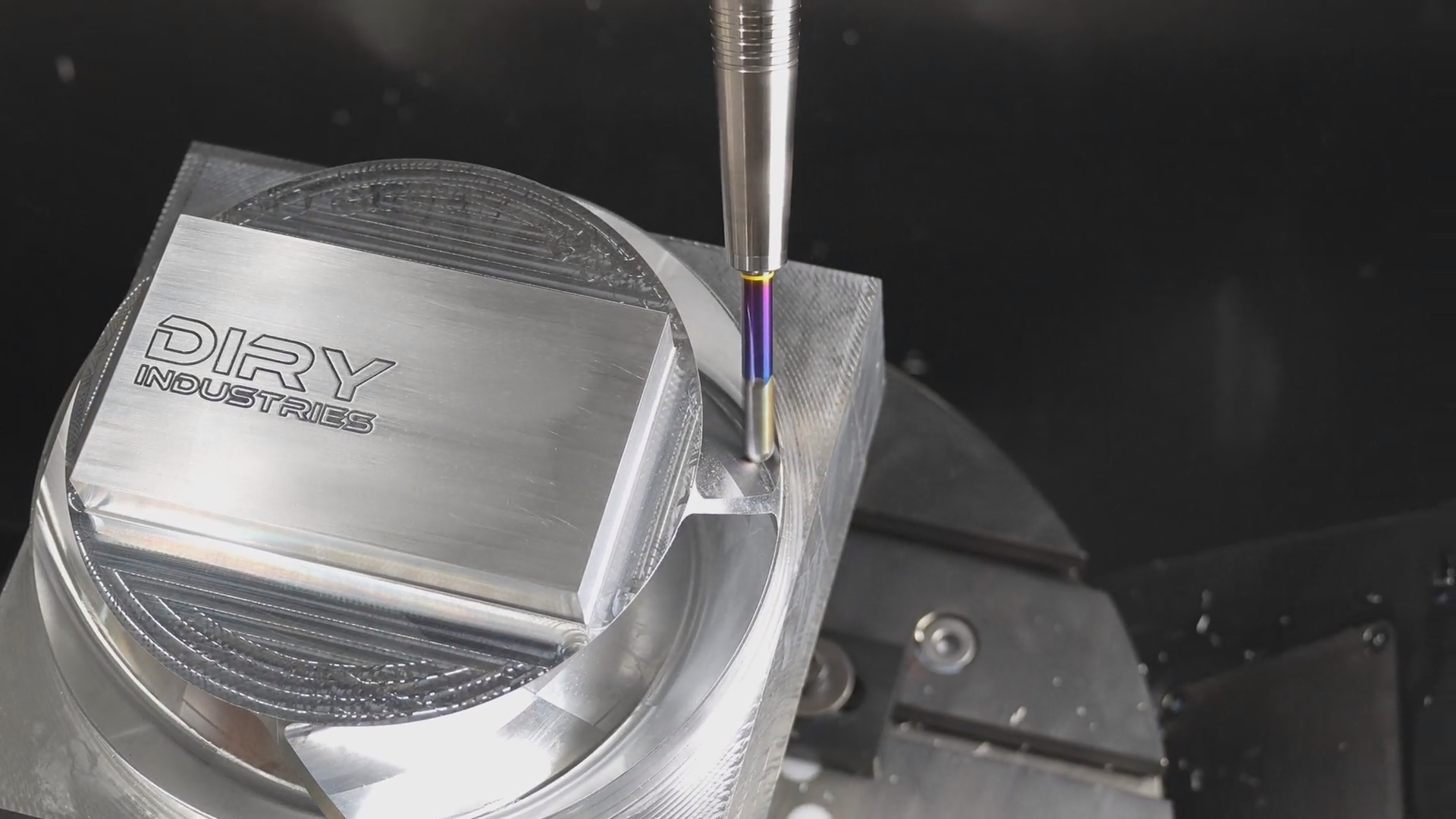
Wir generieren unsere Werkzeugwege und NC-Programme durch führende CAM-Software. Die Konturen der Schaufeln sind dreidimensional gekrümmt und erfordern ständige Winkelanpassungen des Werkzeugs, die Bearbeitung der Freiformflächen geschieht deshalb vorwiegend durch Simultanbearbeitung. Simultanfräsen bezeichnet die gleichzeitige Bewegung von fünf Achsen (X, Y, Z sowie Dreh- und Schwenkbewegungen der Werkzeughalterung) während der Bearbeitung. Im Gegensatz zur 3-Achs-Bearbeitung, bei der das Werkzeug nur linear in drei Richtungen bewegt wird, ermöglicht das Simultanfräsen eine kontinuierliche Anpassung des Werkzeugs an die komplexe Geometrie einer Freiformfläche. Freiformflächen zeichnen sich dadurch aus, dass sie keine regelmäßige Struktur besitzen und keine ebenen oder symmetrischen Bereiche aufweisen.
Test und Validierung unter realen Bedingungen
Einbau und Toleranzprüfung
Nach der Fertigung wurde der neue Impeller in das Jet-Antriebssystem integriert. Dabei wurde besonderes Augenmerk auf die Passgenauigkeit im Antriebskanal gelegt. Diese ist entscheidend, um Strömungsverluste zu minimieren und die Effizienz zu maximieren.
Testfahrt mit Leistungsmessung
Das fertige System wurde in einem Sportboot mit einem 500 PS starken V8-Motor getestet.
Die Ergebnisse zeigten:
- Eine signifikante Steigerung der Höchstgeschwindigkeit.
- Verbesserte Beschleunigungswerte.
- Ein insgesamt ruhigerer Lauf des Antriebssystems.
Diese Ergebnisse bestätigen die Effektivität der durchgeführten Optimierungen.
Fazit
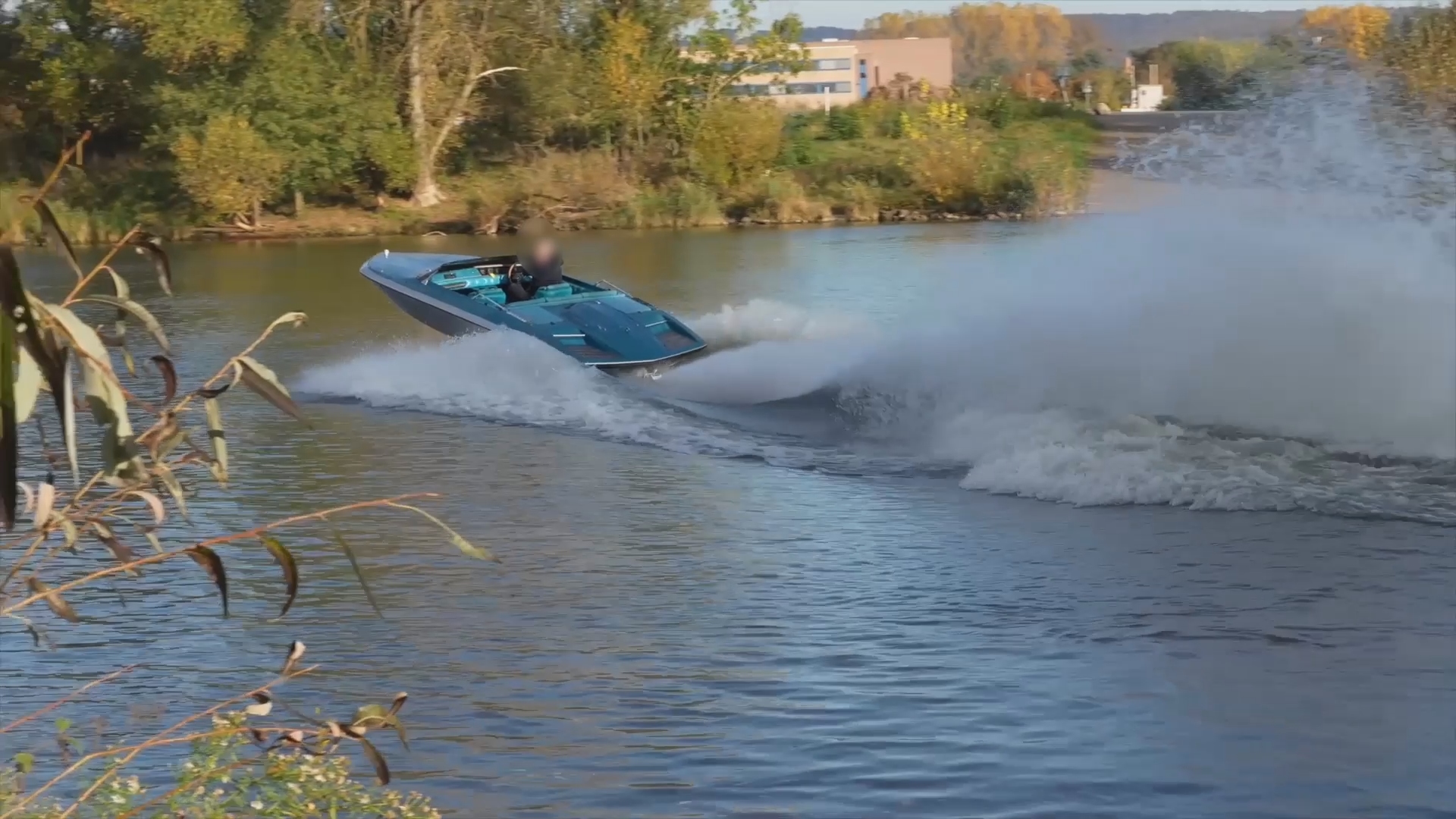
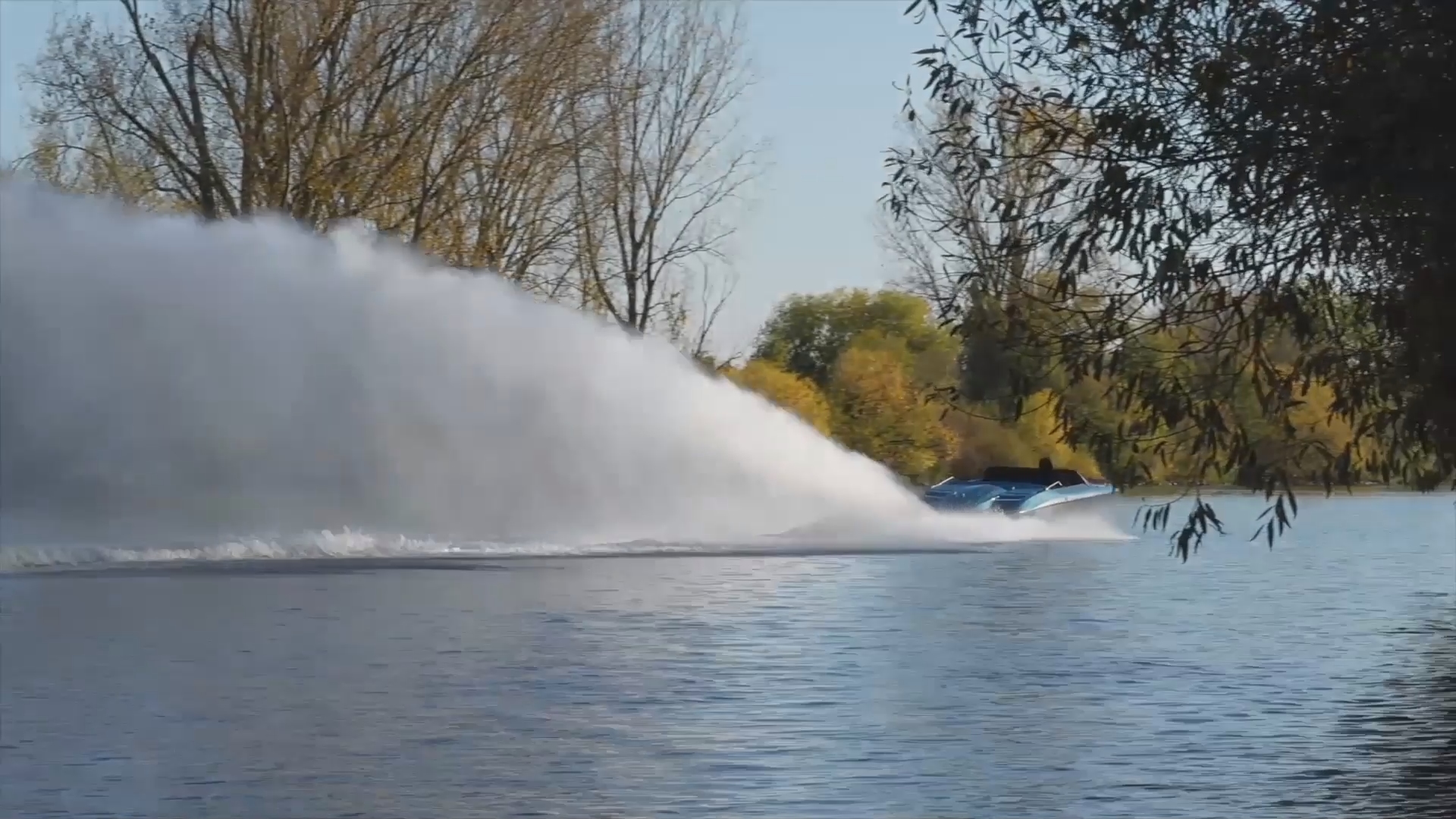
Die Optimierung eines Impellers erfordert ein tiefes Verständnis der Strömungsmechanik, modernste Fertigungstechnologien und die Wahl geeigneter Materialien.
In unserem Projekt konnten wir durch Reverse Engineering, geometrische Anpassung und CNC-Fertigung ein Bauteil schaffen, das den gestiegenen Anforderungen nicht nur gerecht wird, sondern die Leistung des gesamten Antriebssystems verbessert.
Ihre Lösung für die Marine-Antriebstechnik
Sind Sie auf der Suche nach einem Partner, der Ihre Bauteile optimiert und präzise fertigt? Bei Diry Industries vereinen wir Expertise in Reverse Engineering, Strömungsmechanik und CNC-Fertigung, um Ihnen innovative Lösungen zu bieten.